脱氧
铝粉:由于电渣重熔过程在大气下完成,其实际是一个氧化的过程。随着重熔的不断进行,渣池会不断的从大气中吸入氧气,熔池又通过吸收渣中的氧,而产生钢锭含氧量的提高,从而导致冶金质量的下降。
为了降低钢锭中氧的含量,提高冶金产品的质量,通常采取真空电渣重熔、惰性气体保护气氛电渣重熔、电渣重熔渣系多元调整、电渣重熔过程加脱氧剂对氧进行消耗,降低产品中氧的含量。脱氧铝粉与这几种方法比较,真空电渣重熔、惰性气体保护气氛电渣重熔虽能有效的防止钢锭重熔时的吸气、增氧,保证钢锭中氧的含量尽量降低,但对电渣炉的设备有较高的要求,并且生产成本较高;电渣重熔渣系多元调整的生产组织复杂且效果不够稳定;相比来说,加入脱氧剂对生产实力不强,成本较低的中小企业来说是一个不错的选择。脱氧剂的种类繁多,其中脱氧铝粉的效果最好,且原料易得,价格低廉,是使用最为广泛的一种脱氧剂。
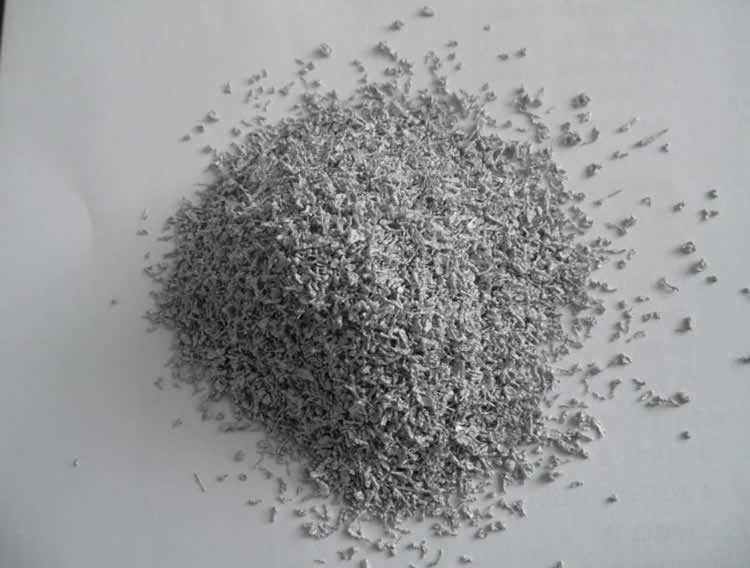
电渣重熔过程脱氧铝粉的加入方法,通过对结晶器中铝粉加入方式的控制,采用不同粒径的铝粉相互配合,对电渣重熔的氧进行消耗,有效降低电渣重熔过程的吸气、增氧,从而降低钢锭中的含氧量,提高产品质量。将不同粒径的脱氧铝粉相隔一定间距均匀地放置在传送装置上,并通过传送装置均匀、连续地加入结晶器。
现有的铝粉作为脱氧剂都是采用分批次加入的方式,会存在脱氧剂的间断,导致冶炼时吸氧不能及时去除,进而进入熔池,导致冶金质量下降。采用不同粒径的铝粉加入结晶器,采用不容粒径的脱氧铝粉相互配合,从而实现电渣重熔过程中脱氧的目的。脱氧铝粉加入方法:首先将小粒度的铝粉均匀地铺放在传送装置上,然后将大粒度的大粒径的铝粉以相隔一定距离均匀地放置在传送装置上。当传送装置工作时,小粒度的铝粉最先被送入渣池,将渣池内的氧进行有效降低,从而防止氧进入熔池;较大粒径的铝粉随着传送装置运行加入结晶器后,由于小粒度的脱氧铝粉已经将渣池内的氧进行降低,渣池对铝粉的消耗量就会降低,大粒径的
铝粒会进行熔池,从而有效地去除熔池中的氧,降低钢锭中氧的含量,提高钢锭的冶金质量及性能。
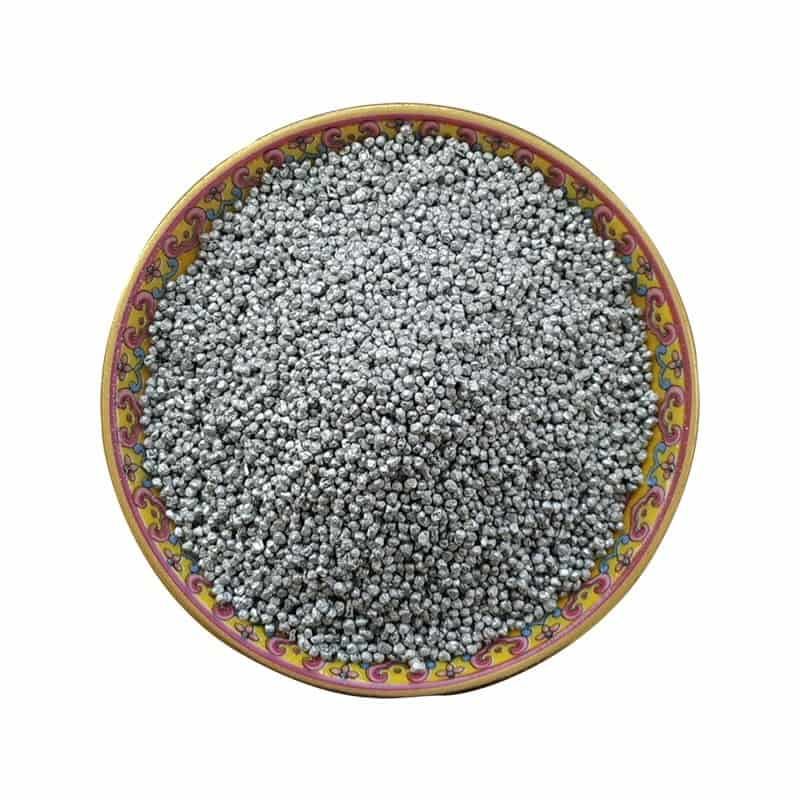
作为本发明一种电渣重熔工程铝粉的加入方法的一个具体实施例,所述不同粒径铝粉的粒径分别为1~3mm、8~10mm。本发明将小粒径的铝粉设置为1~3mm是为了确保其能在渣中迅速与氧反应而不进入熔池,过小的话,由于表体比增大,影响其脱氧效果;过大会进行熔池,达不到本发明小粒径铝粉除渣池氧,大粒径铝粉除熔池氧的目的。本发明将大粒径的铝粉设置为8~10mm,大粒径铝粉主要是为了与熔池中的氧反应,太小进入不了熔池,太大则不会完全熔化,增大钢锭中铝的含量,影响冶金产品质量及效果。
脱氧铝粉粒径为8~10mm的铝粉以每粒相距10~12cm的间距均匀地放置于传送装置上。每熔化40~50kg合金,加入一粒8~10mm粒度的脱氧铝粉效果最佳,间距过大达不到脱氧的效果,太小则容易导致熔池铝含量升高而改变合金的成分。
脱氧铝粉的加入方法,包括以下步骤:
1)将放置铝粉的传送装置用重砣悬挂于电渣炉冶炼支臂上;
2)将粒径为1~3mm的脱氧铝粉均匀铺放在传送装置上;
3)将粒径为8~10mm的铝粉以每粒相距10~12cm的间距均匀放置于传送装置上;
4)电渣启动后,传送装置随冶炼支臂的下降而移动,将传送装置上的铝粉连续、均匀地加入至结晶器。
可以根据脱氧铝粉加入量及生产需求进行调整,下降速度太快铝粉融化太快,脱氧效果差,下降速度太慢则会加大渣池及熔池中的含氧量,不利于氧的脱除,可以根据具体合金生产量及脱氧铝粉加入量的需求进行适当调整。通过铝粉加入装置,将粒度为1~3mm的脱氧铝粉传送入渣池,将渣池内的氧进行有效的降低,从而防止氧传入熔池。当传送至较大粒度(8~10mm)的铝粒掉入结晶器时,较大粒度的铝粒会进入熔池,从而有效的去除熔池中的氧,从而提高钢锭的冶金质量和性能。脱氧铝粉加入方法成本低下,有很好的经济效益,适合推广。